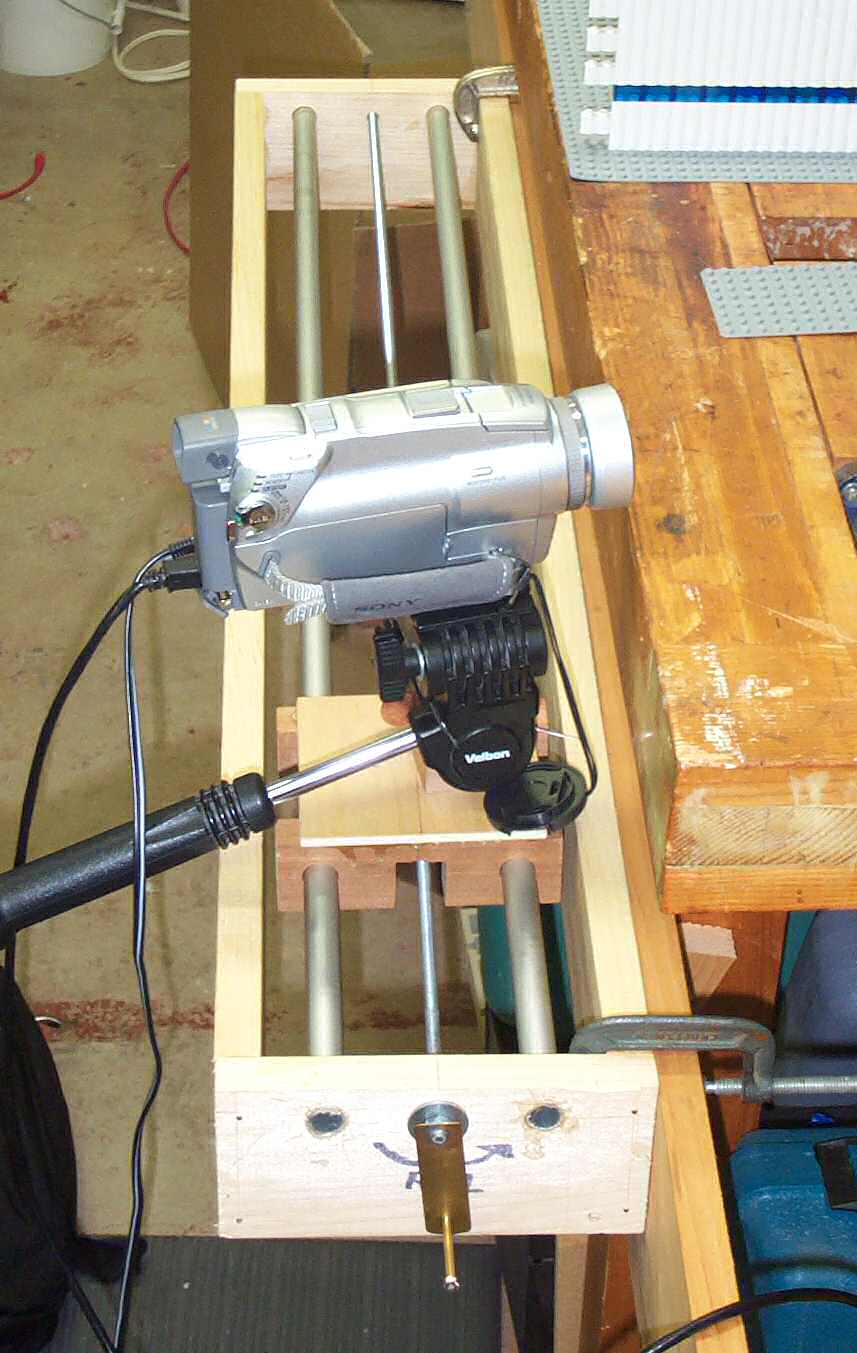 |
Overall view of the dolly. |
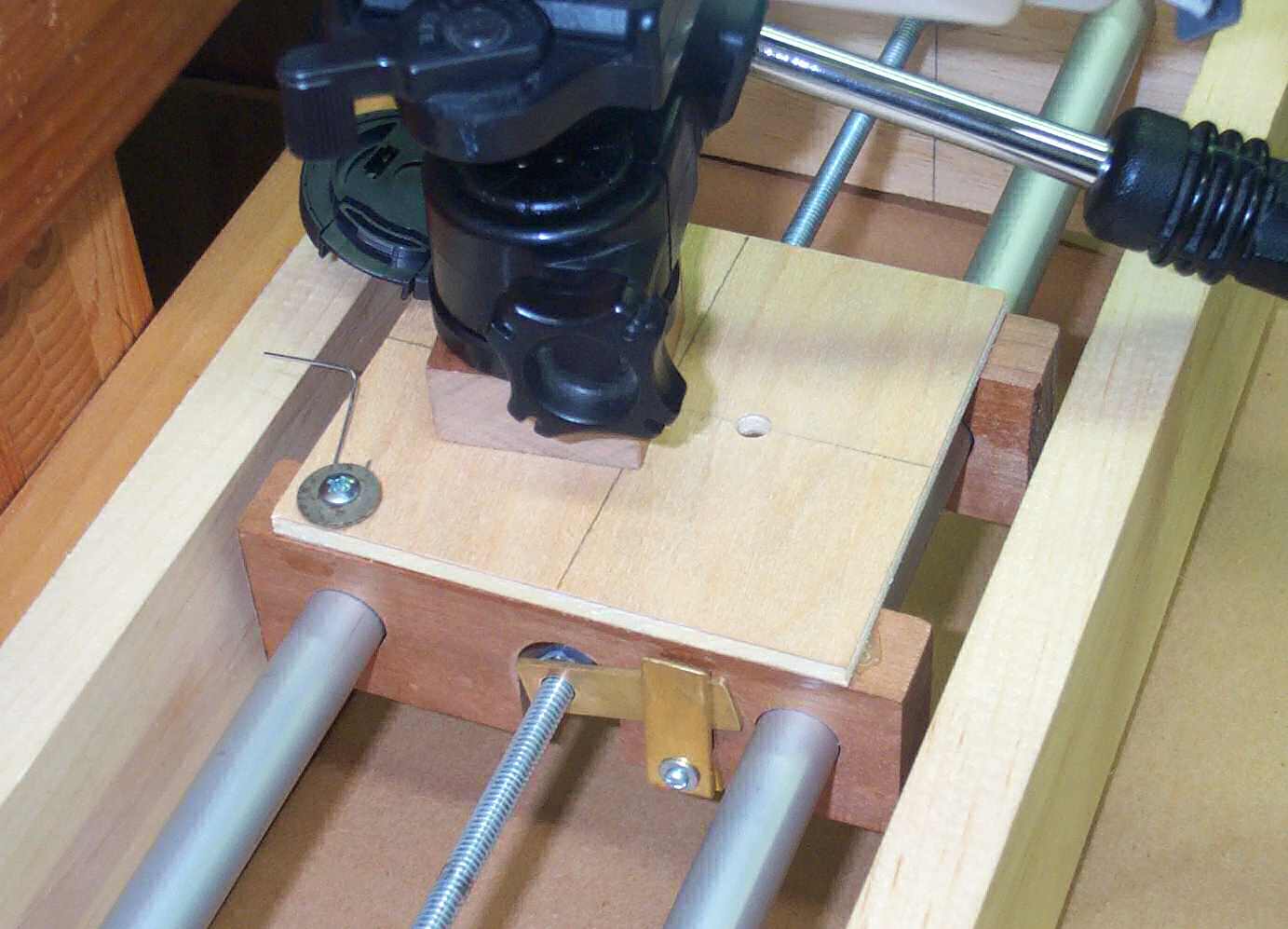 |
Closeup of the car on the rods and the threaded rod. Tripod head can be mounted to the car in a few positions. |
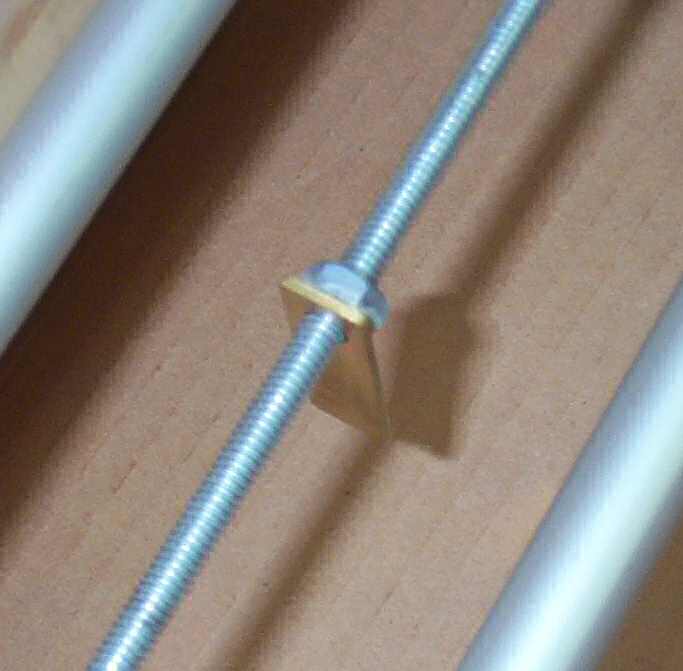 |
Closeup of the nut soldered to the brass tab.p |
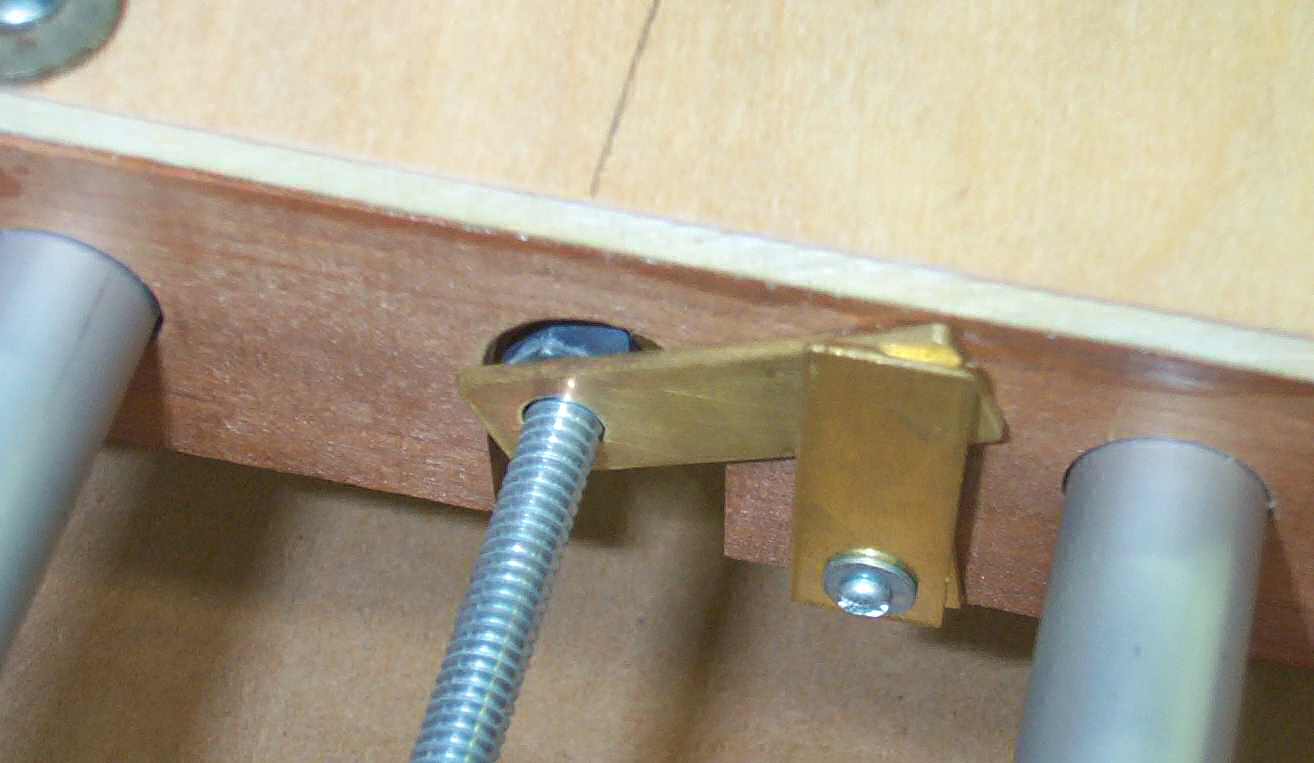 |
Closeup of the quick release mechanism. To not skimp on this step. Without a quick release, it takes
forever to move the camera back and forth to setup and plan the shot. |
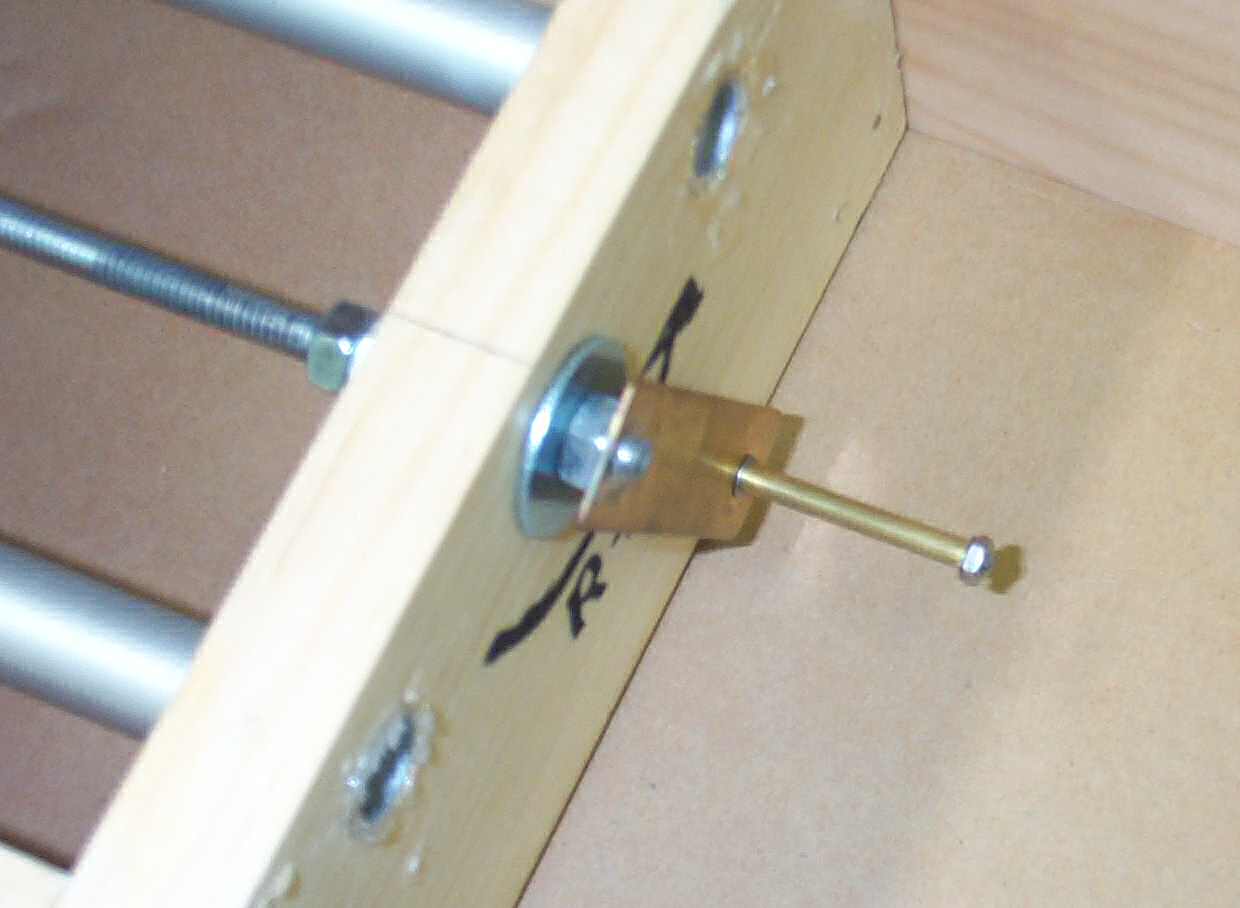 |
Details of the crank. I soldered the brass stock to a nut and the threaded rod. On the inside I used two
nuts tightened against each other as a stop. Used some nice fender washers to reduce friction and wear. |
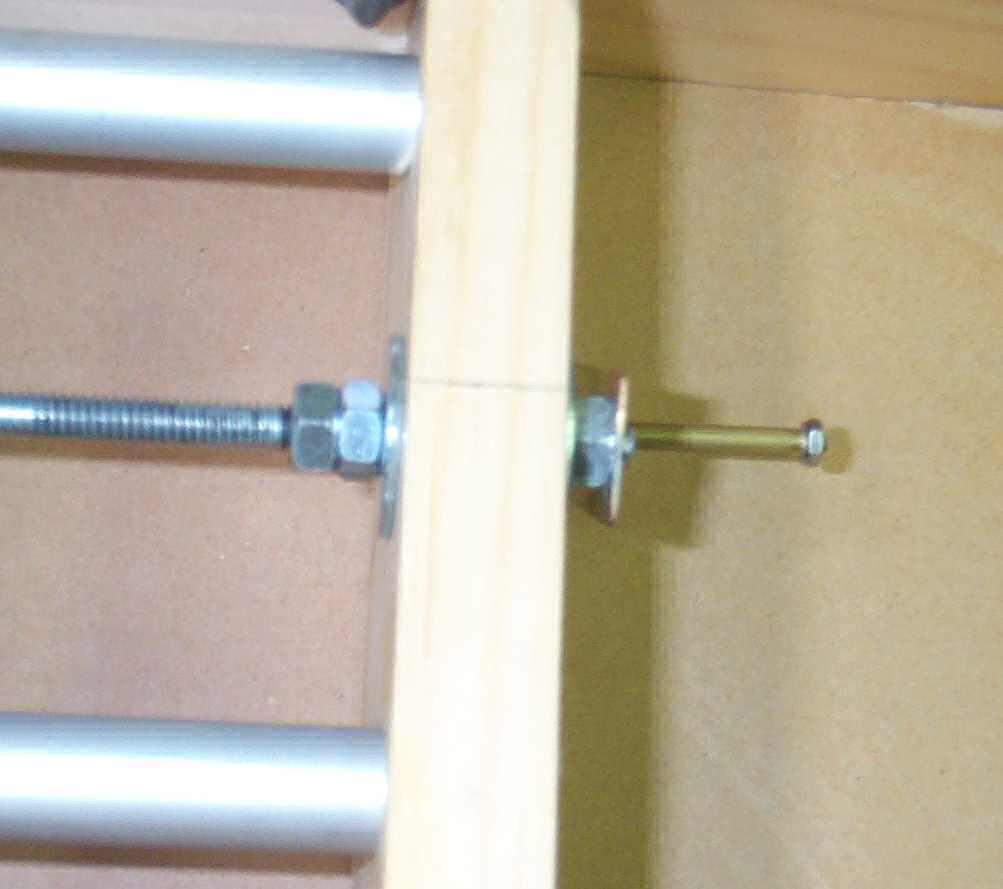 |
More details on the handle. |